Strategies for Streamlining Machinery Parts Manufacturing
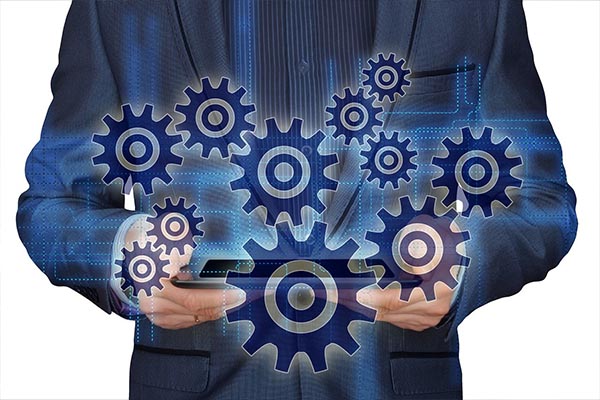
The Ultimate Guide to Machinery Parts Manufacturing
How to Enhance Efficiency and Quality
Are you in the machinery parts manufacturing industry and looking to enhance your efficiency and quality? Look no further! In this ultimate guide, we will provide you with valuable insights and strategies to optimize your machinery parts manufacturing process.
Efficiency and quality are crucial factors in staying competitive and meeting customer demands. By implementing the right techniques and tools, you can streamline your operations, reduce downtime, and improve overall productivity. This guide will cover a wide range of topics, including workflow optimization, maintenance strategies, employee training, and quality control measures.
Whether you are a small-scale machine shop or a large manufacturing facility, this guide is tailored to suit your needs. We understand the challenges you face in this ever-evolving industry, and our goal is to equip you with practical solutions that will help you stay ahead of the game.
So, buckle up and get ready to take your machinery parts manufacturing to the next level. Let's dive into the ultimate guide to enhancing efficiency and quality in your manufacturing process!
Importance of Enhancing Efficiency and Quality in Machinery Parts Manufacturing
In the machinery parts manufacturing industry, efficiency and quality stand as the twin pillars that uphold a successful operation. Enhancing these factors is not merely a goal but a necessity for firms aiming to maintain their competitive edge. Efficient processes reduce waste and ensure that production timelines are adhered to, which is vital in meeting customer demands and maintaining satisfaction. Moreover, the combination of efficiency and quality leads to better resource allocation, ultimately impacting the bottom line positively. Companies that prioritize these elements often experience lower production costs and increased profitability.
Quality is equally critical; it is the benchmark that defines a manufacturer’s reputation. High-quality machinery parts not only meet regulatory standards but also exceed customer expectations, fostering loyalty and repeat business. In an industry where precision is paramount, the implications of subpar quality can lead to significant financial losses and damage to brand reputation. Therefore, investing in processes that enhance both efficiency and quality can create a virtuous cycle, where improvements in one area yield benefits in the other. This interplay is crucial for sustaining growth and ensuring long-term success.
Furthermore, enhancing efficiency and quality contributes to innovation. When manufacturers streamline their processes and focus on producing high-quality parts, they free up resources to invest in research and development. This aspect is essential in adapting to changing market demands and technological advancements. By fostering a culture of continuous improvement, manufacturers can remain agile, respond to market shifts promptly, and explore new opportunities that drive the industry forward. In summary, prioritizing efficiency and quality is not just about immediate gains; it is about laying a solid foundation for future growth and sustainability.
Common Challenges in Machinery Parts Manufacturing
Machinery parts manufacturing is fraught with challenges that can impede efficiency and compromise quality. One of the most prevalent issues is managing production schedules. Delays can arise from various sources, such as equipment breakdowns, supply chain disruptions, or labor shortages. These delays not only affect output but can also lead to increased operational costs and strained customer relationships. The complexity of coordinating multiple processes and resources makes it essential for manufacturers to develop robust scheduling systems to mitigate these risks.
Another significant challenge is maintaining consistent quality across products. Variability in raw materials, equipment wear and tear, and human error can all lead to defects in manufactured parts. Establishing stringent quality control measures is vital to address these issues. However, implementing such measures can be resource-intensive and may require a cultural shift within the organization. Manufacturers must invest in training and technologies that empower teams to focus on quality, ensuring that every part meets the necessary specifications before it leaves the production line.
Moreover, the rapid pace of technological change presents its own set of challenges. Machinery parts manufacturers must continuously adapt to new tools, techniques, and materials, often requiring significant investment. The challenge lies not only in acquiring new technologies but also in integrating them into existing workflows. Resistance to change from employees can further complicate this process. Therefore, manufacturers must cultivate a culture of adaptability and continuous learning, equipping their workforce with the skills and knowledge necessary to thrive in an ever-evolving environment.
Strategies for Improving Efficiency in Machinery Parts Manufacturing
Improving efficiency in machinery parts manufacturing begins with a thorough analysis of current processes. Lean manufacturing principles, which focus on minimizing waste while maximizing productivity, can be particularly effective. By mapping out workflows and identifying areas of waste, manufacturers can streamline operations and implement changes that lead to significant time and cost savings. Techniques such as value stream mapping can help visualize processes and pinpoint inefficiencies that need addressing.
Another effective strategy is to adopt standardized work procedures. By creating clear, documented processes for each task, manufacturers can reduce variability and ensure that everyone is on the same page. Standardization not only facilitates training but also enhances accountability among team members. When employees understand their roles and responsibilities clearly, it leads to smoother operations and less downtime. Regular reviews and updates to these procedures can also help keep them relevant and effective in a changing environment.
Investing in automation and advanced manufacturing technologies is another way to enhance efficiency. Automated systems can take over repetitive tasks, freeing up human resources for more complex activities that require critical thinking. Technologies such as CNC machines, robotics, and IoT devices can significantly increase production rates and accuracy. However, integrating these technologies requires careful planning, training, and sometimes a cultural shift within the organization. Manufacturers must approach this investment strategically, ensuring that they are not only adopting new technologies but also aligning them with their overall operational goals.
Techniques for Enhancing Quality in Machinery Parts Manufacturing
Enhancing quality in machinery parts manufacturing requires a multifaceted approach that encompasses various techniques. One effective method is the implementation of Total Quality Management (TQM) principles. TQM fosters a culture of continuous improvement, emphasizing the importance of quality at every level of the organization. By involving all employees in the quality assurance process and encouraging feedback, manufacturers can identify areas for improvement and implement changes that lead to higher quality outputs.
Statistical Process Control (SPC) is another valuable technique for monitoring and improving quality. By using statistical methods to analyze production data, manufacturers can identify trends, variations, and potential issues before they escalate into significant problems. Implementing SPC requires investment in training and tools, but the payoff can be substantial. By proactively addressing quality concerns, manufacturers can reduce defects and rework, ultimately saving time and resources.
Regular audits and inspections are essential for maintaining high-quality standards. By conducting routine assessments of processes, equipment, and products, manufacturers can ensure compliance with quality standards and identify any deviations early. These audits can also serve as training opportunities, helping employees understand the importance of quality and the role they play in achieving it. By fostering a culture that prioritizes quality, manufacturers can motivate their teams to strive for excellence consistently, resulting in improved product quality and customer satisfaction.
Utilizing Technology in Machinery Parts Manufacturing
The integration of technology in machinery parts manufacturing has revolutionized the way companies operate. Advanced technologies such as CAD (Computer-Aided Design) and CAM (Computer-Aided Manufacturing) allow for precise design and efficient production processes. These tools enable manufacturers to create complex parts with high accuracy, reducing the likelihood of errors and rework. The adoption of these technologies can significantly enhance both efficiency and quality, allowing manufacturers to respond more swiftly to market demands.
Moreover, the Internet of Things (IoT) is playing an increasingly vital role in machinery parts manufacturing. IoT devices can provide real-time data on equipment performance, enabling manufacturers to monitor their machinery closely. This capability allows for predictive maintenance, where potential issues are identified and addressed before they lead to equipment failure. By reducing downtime and maintenance costs, manufacturers can improve overall operational efficiency and extend the lifespan of their machinery.
Artificial Intelligence (AI) and machine learning are also transforming the landscape of manufacturing. These technologies can optimize production schedules, manage inventory, and even predict market trends. By analyzing vast amounts of data, AI can identify patterns and make recommendations that enhance decision-making processes. Incorporating AI into manufacturing operations can lead to more efficient workflows, reduced waste, and improved quality control measures, ultimately driving profitability and competitiveness.
Best Practices for Machinery Parts Manufacturing
Implementing best practices in machinery parts manufacturing is essential for achieving sustained efficiency and quality. One foundational practice is the adoption of lean manufacturing principles. By continuously assessing and refining processes to eliminate waste, manufacturers can streamline operations and improve productivity. This practice not only reduces costs but also fosters a culture of continuous improvement, encouraging teams to seek out innovative solutions to operational challenges.
Another best practice involves establishing a robust quality management system (QMS). A QMS provides a structured approach to managing quality throughout the manufacturing process. By defining clear quality objectives, conducting regular audits, and ensuring compliance with relevant standards, manufacturers can maintain high-quality outputs consistently. Additionally, involving employees in the QMS process can instill a sense of ownership and accountability, further enhancing overall quality.
Collaboration and communication across departments are also critical best practices. By fostering an environment where teams work together and share information, manufacturers can address challenges more effectively. Regular cross-functional meetings can help identify potential issues early and facilitate the sharing of ideas and solutions. This collaborative approach not only improves efficiency but also enhances the quality of the final product, as various perspectives contribute to problem-solving and innovation.
Tools and Equipment for Efficient and High-Quality Manufacturing
Selecting the right tools and equipment is crucial for achieving efficiency and quality in machinery parts manufacturing. High-precision machines, such as CNC (Computer Numerical Control) machines, are essential for producing complex parts with tight tolerances. These machines offer automation capabilities that increase production speed while maintaining accuracy. Regular maintenance and calibration of these machines are vital to ensuring they operate at peak performance.
In addition to machining equipment, investing in advanced measuring tools is essential for quality control. Coordinate measuring machines (CMM) and laser scanning systems can provide accurate measurements of components, helping to identify defects quickly. These tools can facilitate rapid feedback loops, enabling manufacturers to make necessary adjustments in real-time, thereby reducing the likelihood of producing defective parts.
Additionally, utilizing software solutions designed for manufacturing can streamline operations significantly. ERP (Enterprise Resource Planning) systems can integrate various aspects of the manufacturing process, from inventory management to production scheduling. By providing real-time data and analytics, these systems help manufacturers make informed decisions that enhance efficiency and quality. The right combination of tools and equipment, paired with effective software solutions, can significantly elevate a manufacturing operation's overall performance.
Training and Skill Development for Machinery Parts Manufacturing
Investing in employee training and skill development is paramount for enhancing efficiency and quality in machinery parts manufacturing. A well-trained workforce is better equipped to operate advanced machinery, adhere to quality standards, and adapt to new technologies. Manufacturers should implement continuous training programs that cover not only technical skills but also soft skills, such as problem-solving and teamwork. These holistic training initiatives foster a culture of excellence and adaptability among employees.
Hands-on training is particularly effective in the manufacturing environment. By allowing employees to engage directly with machinery and tools, manufacturers can reinforce learning and improve retention. Mentorship programs can also be beneficial, pairing experienced employees with newer team members. This approach not only accelerates the learning curve for newcomers but also strengthens team dynamics and knowledge sharing within the organization.
Furthermore, fostering a culture of continuous improvement is essential for skill development. Encouraging employees to pursue certifications, attend workshops, or participate in industry conferences can enhance their expertise and keep them informed about the latest trends and technologies. By prioritizing training and development, manufacturers can build a knowledgeable and skilled workforce that drives efficiency and quality in the production process.
Conclusion: The Future of Machinery Parts Manufacturing
As the machinery parts manufacturing industry continues to evolve, the focus on enhancing efficiency and quality remains paramount. Companies that embrace innovative technologies, adopt best practices, and invest in employee development will be well-positioned to thrive in an increasingly competitive landscape. The integration of automation, IoT, and AI will only accelerate the drive toward greater efficiency and higher quality standards.
Moreover, the importance of sustainability cannot be overlooked. As manufacturers seek to optimize operations, they must also consider the environmental impact of their processes. Implementing eco-friendly practices and materials will not only meet regulatory requirements but also respond to the growing demand for sustainable manufacturing solutions. Companies that prioritize sustainability alongside efficiency and quality are likely to gain a competitive advantage in the market.
In conclusion, the future of machinery parts manufacturing lies in the ability to adapt to change while maintaining a relentless commitment to quality and efficiency. By continuously assessing and improving processes, leveraging technology, and nurturing talent, manufacturers can navigate the challenges of the industry and emerge as leaders in the field. The journey toward excellence is ongoing, and those who invest in their operations today will reap the rewards of success in the years to come.